Here’s a cool photo I grabbed after a dyno run! Shows what kind of heat goes through the manifold
And here’s the picture you’ve all been waiting for:
First of all – you’ll all look at the power figure and think that’s fairly low. and so did I. A TD06 at 1.4bar/20psi should be over 400hp on a strong motor! I was a bit underwhelmed/disappointed to be honest. I built the whole setup to flow and work together, so an aim of 400whp would be quite a realistic goal. As for the low power figure, we’re not entirely sure either. The way the car pulled on the dyno was nothing like a 340hp motor; it’s nothing short of savage.
The obvious theory is the dyno – as we all know, dyno’s vary from place to place. But Paul SR22 made 500hp previously, which is the power region his setup should be making. Could it have been in a wrong mode? Or was the car strapped incorrectly – as this can play with the power figures also..
The next idea was the rear alignment – with the wheels potentially pulling in different directions, could that affect the end power reading? Or the bouncy rear end – could that have meant the full power wasn’t being put down?
The motor seems to breathe nicely – it has perfect AFR’s across the entire rev range up to the 7600 rev limit. We pulled the plugs out after mapping to check them, and all of them have a super clean & equal burn.
If I remember correctly, Paul’s car made 500+hp at 74(?)% injector duty cycle – mines running 62% so it’s not a mile off. Martin did the maths – a combination of using the amount of fuel the engine is taking, and multiplying it by the amount of horsepower the SR uses (this is probably incorrect, but he did some mathematical wizardry) and said the engine is taking enough fuel for the 420hp mark. Odd! He told me to have faith that it’s 400hp setup – so the plan is to take it out on track and see just how hard it pulls!
The cool thing about the graph is how linear it is - TD06’s are notoriously “laggy”. Not on this motor

It comes on boost fast and hard, more encouraging signs it’s a strong and well built motor!
The noise this thing makes is crazy. Like really crazy. Paul’s S14a was pretty damn loud, but this thing on full chat was on another level. The sound is literally to die for, it has a very angry and purposeful TD06 sound to it.
In regards to the oil leak mentioned earlier – I noticed that after the oil change it was much less frequent than before. My thoughts were now the rear crank seal, perhaps the mineral oil was too thin when warm and passing through a seal? However, there was still a slight drip when running 15w50 synthetic oil. I could either leave it be, and hope for the best. Or remove the gearbox and re-seal the area. Personally, I think the latter is the most likely option. I just don’t want to risk ruining a clutch nor an engine over a leak.
So after a really really long day – I finally made it home after battling torrential rain, Devon’s finest inclines in the dark!
- - - Updated - - -
I didn’t get home until the early hours of the morning – so set upon unloading it the following morning. What a contrasting day in terms of the weather!
Another theory was the cam timing – maybe it could have been off due to the VVT Delete – but Dave and Martin checked this after mapping to which its perfect.
My freshly built 4.08 vs my old Nismo 4.36:
- - - Updated - - -
Now mapping had finished – I could finally lower the rear end! (I really couldn’t tell you how much I wanted this day to come!)
So, mapping highlighted a few areas which need to be addressed. The first being the oil leak, the 2nd was to increase the cooling efficiency of my setup. With my current setup, everything should be spot on. But, I guess with mapping the car is stationary so heat soak has an even larger effect. After a few dyno pulls, the intake temps soared. Time to get this addressed!
First things first – I’ve created a slight gap between the radiator and intercooler. My thinking here is that with these touching, the radiator is just heating the rear of the intercooler. With a slight gap thank to a thin strip of dense foam, only the very sides of one another are actually touching, which should help rectify this issue.
The intake pipe was also getting warm – again, an area where heat soak had obviously taken place due to the car being stationary. I keep thinking about reflective heat wrap and wrapping the downpipe back, but one idea was to introduce a cold air feed from the bumper to the filter – making sure the filter has a nice supply of fresh air. And if done right, would be a cool subtle addition.
In a bid to help reduce air intake temps, I’ll probably run the car without side lights for a little while. Whilst it’s a small change, it’ll introduce more fresh air to the engine bay and hopefully help lower those AIT’s!
Next up was trying to gain a bit more clearance up front as I’ve already cracked the front wing due to the front caster settings which are just random. I’ve decided to drop down to a 225/35 which should gain me that extra few mm clearance I need. Plus, it’ll also help to lower the front end.
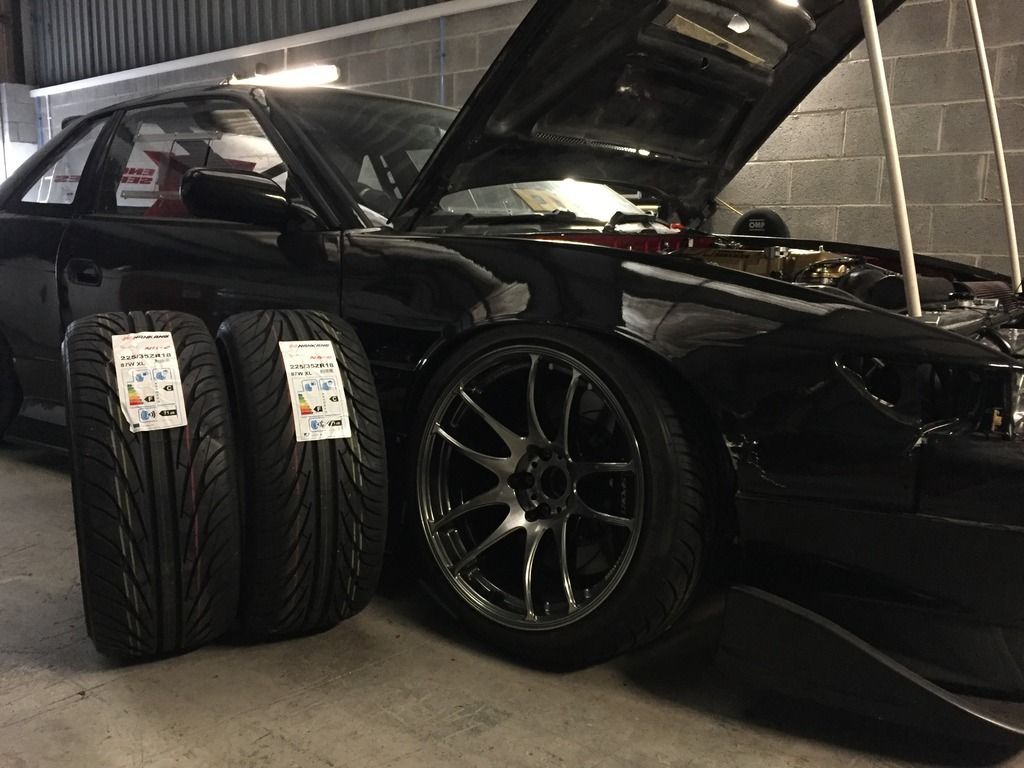